A stepper motor is a 2-phase brushless DC motor designed to rotate the shaft through a series of small steps. Each step is the result of individual electrical pulses delivered by a stepper drive. Stepper motors are most often used in an open-loop system design. Unlike a servo system, no encoder or other feedback device is required. Instead, positional control is achieved as the drive counts the number of step commands from a known starting point.
What is a Stepper Motor?

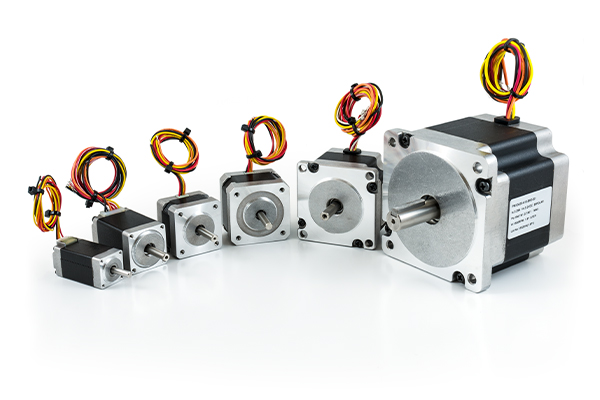
How Does a Stepper Motor Work?
Also known as step or stepping motors, the design of these motors divides each full rotation into a series of equally sized steps — usually 200 — to enable quick, precise load positioning and exceptional holding torque at any individual step. When using a microstepping drive, each step can be divided into even smaller increments — approaching the unlimited positioning control that can be achieved with a servo motor, but without the need for complex feedback devices or a closed-loop control system.
Stepper motors achieve their positioning control by means of permanent magnets mounted on the rotor, driven by two winding phases on the stator. Fine teeth on the rotor and stator laminations control the angle of each step. As the stepper drive reverses the current in each winding in sequence, the rotor advances step by step, allowing precise position control with reference to a known starting point.
Stepper Motor Features
Step angle. Most stepper motors have 200 teeth, resulting in 1.8º of rotation with each full step (360º / 200 = 1.8º). Finer steps can be achieved through more sophisticated control of the DC power applied to the motor. For example, positive current, no current, and negative current applied to each winding in succession results in half-step angles of 0.9°. Fine control over the amount of current sent to the individual windings can achieve “microstepping” increments as small as 1/250 of a full 1.8°step for nearly servo-like performance.
Unipolar versus bipolar. Unipolar stepper motors have two coils with a shared center tap. The ends of each coil are alternately connected and disconnected to create a rotating magnetic field. Only one coil is energized at a time. Bipolar stepper motors have two coils with independent leads that can be simultaneously energized, with the current reversed between them. This requires a more sophisticated drive, but provides performance advantages such as higher dynamic and holding torque due to the greater magnetic energy that is always present.
DC versus AC. Most stepper motors run on a DC power supply from the drive. However, AC stepper motors are also available. These are synchronous motors, with rotational speed directly proportional to the AC frequency — for example, at 120 VAC 60 Hz, the motor will turn at 72 rpm. This speed can only be varied by changing the AC frequency or through the use of a gearing system. In contrast, the speed of a DC stepper motor is determined by the variable pulse rate supplied by the drive electronics.
Hybrid stepper motors versus other types. Variable reluctance stepper motors feature a simple design with a non-magnetic, toothed rotor that is only attracted to the wound stator when the latter is energized. Noisy and low in torque, these are rarely used in industrial applications.
Permanent magnet stepper motors, often referred to as “can stack” motors, incorporate permanent magnets with alternating north and south poles on the rotor, and two stacked stator coils or “cans.” Typical step angles are 3.6º, and these motors operate at relatively low torque and speed.
Hybrid stepper motors pair a toothed permanent magnet rotor with a toothed electromagnetic stator. These are generally the most useful stepper motors for industrial applications because they allow significantly higher resolution as well as greater dynamic and holding torque than the other designs, with a wider useful speed range.
Easy setup. Because stepper motors require no encoders or other feedback devices, and no feedback cable, they are significantly easier and more cost-effective to set up and tune than servo motors. Without feedback, however, the system must calculate rotor position from a known starting point.
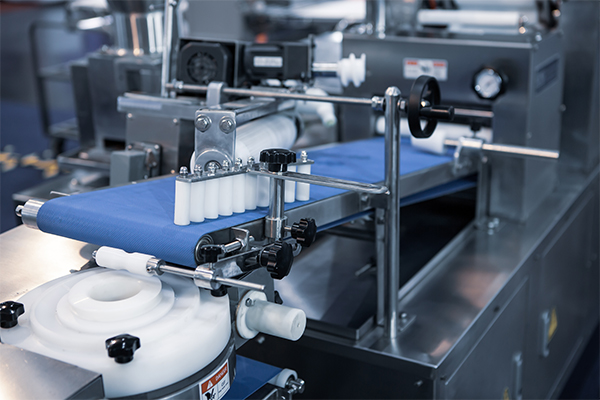
What is a stepper motor used for?
Stepper motors are commonly used across a wide variety of industries due to their precise positioning capabilities and high torque output. Typical stepper motor applications include:
Manufacturing and robotics. Highly repeatable processes, such as indexing operations involving loads with relatively fixed mass, are an ideal application for stepper motors.
Machine tools and metal forming. Stepper motors offer cost-effective motion control for material handling, shaping, grinding, drilling and other applications.
Healthcare. Stepper motors offer dependable, controlled motion for ventilators, pumps, laboratory analyzers, vaccine and pharmaceutical production lines, and more.
Printing, packaging & converting. Web handling, cutting, laminating, folding, embossing and similar processes can often benefit from simple, cost-effective stepper motion.
Stepper systems are also an appropriate choice for many other industries and applications. Let’s discuss your specific motion requirements and find the best solution.
Stepper versus other motor technologies
Stepper motor versus servo motor. Stepper motors move through a fixed number of steps per rotation, controlled by discrete pulses from the stepper drive. Servo motors do not have these fixed steps. Instead, they use a feedback device and data cabling to report rotor position to the drive, which continually adjusts current to correct any positioning errors. Learn how to choose.
Stepper motor versus induction motor. Induction motors have historically been used for single-speed applications, such as conveyors. Although modern induction motors and drives can incorporate feedback, stepper motors are usually a better choice achieving nearly servo-like control without the need for feedback devices.
Stepper motor advantages and disadvantages. Stepper motors are a cost-effective solution for applications that require precise point-to-point positioning of relatively constant and stable loads. Stepper motors can also be advantageous when the application requires high holding torque. Stepper systems are easy to set up and tune, but may not be the optimum choice for varying and unpredictable loads that can cause missed steps and affect machine operation.
A servo system is likely the better choice for more highly dynamic applications that require high-bandwidth disturbance correction, higher speeds and higher continuous and peak torques over the entire speed range. Servo systems provide the greatest possible positional accuracy, speed control and dynamic response.
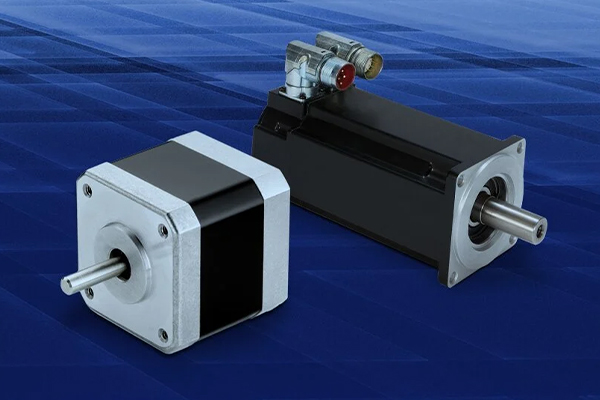
Get Help With Your Application
Kollmorgen’s collaborative engineering expertise is unmatched in the motion industry. We have been an innovation leader for more than 100 years, and have decades of experience serving each industry that benefits from stepper or servo technology. Let us help you engineer the exceptional.