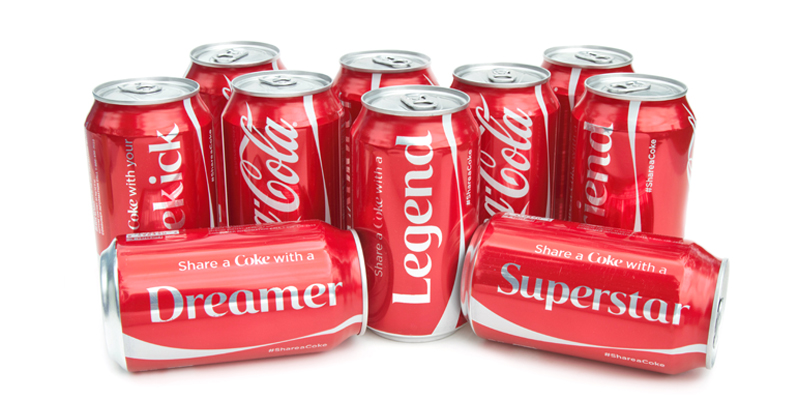
行业和市场趋势
现在,消费者只需点击几下鼠标,按下一个按钮,就可以基于一个相机应用来订购定制眼镜、3D 编织机制作的定制外套和按照模型制作的鞋履。这就是大规模定制,它不仅在改变消费者的购物方式,也在改变商品的制造方式。但对于寻求提供个性化功能的制造商而言,要想真正实现从大规模定制和单件生产,需要的不只是要购买最新的 3D 打印机或设备而已。更为重要的是,要了解整个供应链,而这涉及产品的构思、设计以及制造和物流。
新技术推动旧概念
大规模定制并不是一个新的概念。丰田在 80 年代末期就用过这个概念,耐克在 90 年代末期也将它引入了市场。但是,新技术正在改变消费者的行为,使得消费体验加速迈向更具互动性、个性化和按订单生产的形式。过去的定制要在销售单上勾选几个选项,而现在已经变得更具参与度和个性化,无论是食品与饮料、药品、汽车还是服装。
而推动这一趋势的正是消费者行为和制造技术的演变。消费者正在利用移动技术来实现个性化的购买体验,这也在改变传统供应链(以及围绕可持续发展的对话)。OEM 厂商也在创造更先进的机器,能够进行更精确和复杂的动作,按照消费者的需求定制个性化产品和交货方式。从这个角度看,是消费者在前面,拉动着 OEM 和制造商走向大规模定制化的道路。这对消费者而言无疑是福音,然而也影响了制造商的设备综合效率 (OEE),但如果 OEM 厂商提前做好规划,也可从中获得意外的收益。
OEM 正在追赶消费者
压力现在落在 OEM 身上,OEM 必须做出反应。但这可不像拨动开关那么简单。过去,制造商会针对长期生产周期进行优化,形成大批量产出。而每次转换需要关闭生产线,清洁生产线,替换各种组件。这个过程不仅费时、昂贵,还会拖延产品上市时间。印刷、包装、填充和码垛领域的公司现在更频繁地接到大规模定制的任务,要满足供应链中其他公司的个性化需求。如果能够在不关闭生产线的情况下进行即时更改,就可以大大提高 OEE 并做出更快的市场反应。
举个例子,一家制造商正在生产 20,000 件标准包装的瓶子。但是一家零售商想要运作当下的一个活动,订购了 5,000 件定制包装的瓶子,要求送到指定地点。整个供应链的所有制造商,从印刷到装运,都需要按需生产。理想情况下,制造商可以暂停当前的生产运行,直接连接到客户管理系统,进行即时更改。只要生产不停,制造商就会看到 OEE 效率的直接提高,同时还满足了所有的订单需求。
OEM:新一代设备
通过实施从大规模定制和单件生产,生产线可以将灵活性引入到制造流程当中,及时响应消费者的需求,但也在可用性、性能和质量方面对生产周期造成了巨大的压力。对可用性、性能和质量的衡量是 OEE 的基础:
- 需要进行新的生产批次时,机器要减少计划生产时间的损失。
- OEM 需要了解实际的机器和生产速度并确保其按设计执行。
- 在批次的轮转过程中,必须确保所生产的商品数量达到要求的配额和预期质量,这一点至关重要。
为此,需要新一代的自适应机器来适应产品,而不是让生产顺序固定不变的流程来适应机器。机器需要符合关键的数字商业模式,比如按订单生产、电子商务和直接面向消费者等,同时还要在进行单件生产时具有成本效益。自适应机器需要能对生产线上的每件产品或套件进行独立控制和同步操作。而这需要转变传统的机器观念,开始将机器看做机电一体化应用,将机械、电气、电子和软件融合到即用型模块中。
一切始于(大)数据
消费者正在推动大规模定制的浪潮,而这波浪潮基于海量生成的数据。工业 4.0 和自适应机器背后的基本思想是对数据本身及数据在系统(乃至供应链)中的交换方式进行标准化处理。数据不仅包括来自生产之外(即消费者)的数据,也包括在生产过程中产生的数据。通过在边缘分析数据,制造商能够以内部流程的形式或从另一台机器实时地评估和调整机器性能。边缘分析无需将数据发送到云端进行处理,允许数据集成到资源规划系统中,从而实现更好的规划和灵活性。
构建自适应机器
OEM 在设计机器和考虑提供何种增值服务时,应始终以用户为导向。为了能够实现大规模定制和单件生产,机器需要通过填充、印刷、包装或码垛来量身定制产品。尽管当前的设置可能会使动态定制变得困难,但作为大规模定制的副产品,OEM仍可以设计他们的机器,以跟上不断增加的sku数量。OEM 可以在满足 OEE 目标的同时提高生产灵活性。
伺服小型化
说到电机,当前的趋势是向着伺服小型化方向发展。十五年前,一般的伺服装箱机可能有四个伺服轴。而如今,一个装箱机可能有 16 到 20 个轴,使得打褶、折方、压缩和样式更改等功能都能由伺服驱动。小型化伺服驱动器正在促进新功能的增加,提高流程的自动化并使 OEM 能够实现产品的差异化。
鉴于反馈、功能、电源要求和控制方案的各种排列组合如此之多,一体适用的伺服驱动器解决方案是不存在的。OEM 可能需要混合搭配反馈设备、通信协议和电机功能。比如,无框电机可以在铰接点直接嵌入运动,从而消除齿轮箱、皮带和皮带轮等不必要组件的多余体积和重量。但为了真正保证高质量的生产,伺服轴、CNC 和机器人系统之间需要实时同步。
提升控制水平
除了差异化运动控制系统的机械方面,在实现大规模定制的过程中,还要保障连接性。系统的连接性要确保所有设备的互连。比如,当系统的控制器收集数据时,它可以使用数据来控制系统并按需要与上游设备共享数据。
传统上,机器使用可编程逻辑控制器 (PLC) 来处理离散信息和输出信号以及随后的序列程序。一个单独的运动控制器通过现场总线连接到 PLC,用于控制伺服驱动器。这种设置适用于长期批量运行。而在敏捷数字制造中,要求机器控制器能够并行执行更复杂的任务。这促进了可编程自动化控制器 (PAC) 的发展,使得 OEM 能够针对工业 4.0 准备生产设备。一个集成了逻辑和过程控制、运动控制、可视化、高级编程语言和软件开发工具的单一闭环硬件平台,可以解决接口问题,并推进模块化设计原则,包括大规模定制和单件生产。选择下一代控制平台时,要符合 IEC61131-3 和 PLCopen 等行业标准,并寻找可以与 Ethernet TCP/IP (HTTP API)、Profinet、EtherNet/IP 和 EtherCAT 通信并作为网关的控制系统,从而降低风险。
对于制造商而言,整个系统的开放式连接使得企业资源规划 (ERP) 软件与运动控制系统可直接通信,并能够在个体机器层面或整体生产系统上按需调整生产。出错的几率也会减小,因为数据是系统自动传输而非手写或打印的,不会有写错数字或者因为“粗手指”而在键盘上打错字的可能性。这种稳定且互联的流程可以产生更高的质量、更低的出错率、更大的产量,从而实现更好的 OEE。
不要为了速度而牺牲质量
定制制造面临的挑战是要在整个产品周期中保证质量。迅速、灵活固然好,但不能以牺牲质量为代价。要实现产品的可变生产,需要灵活和集成化的先进检查与跟踪系统。比如,可以使用先进的视觉系统、串行化和跟踪技术来优化日益复杂的印刷、填充、包装和码垛流程。使用大数据、先进的伺服电机和开放的通信协议后,可以在整个生产过程中建立一致性,实现高重复性,而且当生产线某处出现错误时,系统也能及时通报。
从大批量到单件生产
这一目标可能让人畏惧不前,但其实制造商不必进行成本高昂的工厂全面改造,也可以保持竞争力。他们可以与 OEM 伙伴合作,开始将运营方向转向大规模定制,最终达到单件生产。
- 确定哪些生产领域会受益于自动化程度更高的系统
- 战略性地规划设备报废流程并按需要升级和添加设备
- 与运动控制供应商(比如科尔摩根)合作,确定如何迅速高效地进行优化定制,设计出差异化的机器运动控制系统。
OEM 面临着来自制造商(和消费者)不断增长的定制化请求,同时也发现商用 (COTS) 运动控制产品的供应不足。与工程领导者合作有助于解决这一问题。OEM 可以携手科尔摩根的联合工程专家来实现简单、强大的运动控制和自动化。科尔摩根拥有先进的工具、培训和支持作为后盾,可协助整条供应链缓解大规模定制和单件生产所带来的压力。